Quality Control Department
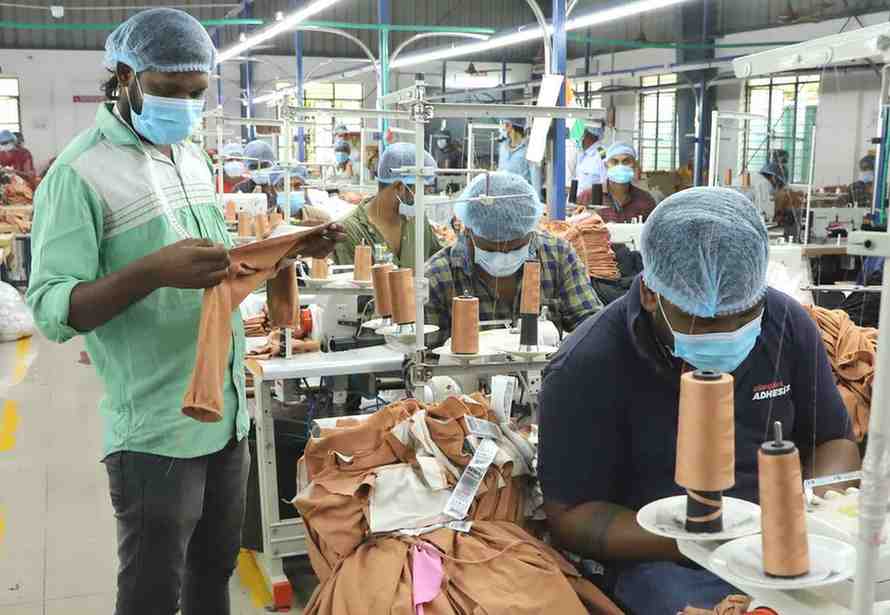
Quality Checking
The quality control department ensures that textile products meet the quality criteria and specifications of the customers and the industry. They inspect the raw materials, fabrics, accessories, and finished products for any defects or deviations.
They also monitor and control the quality parameters such as color fastness, shrinkage, pilling, etc. throughout the production process .
The quality control department is the guardian of the textile industry.
Metal Detector Machine
We use a needle and metal detection system that scans every garment we produce with high sensitivity and accuracy.
It alerts us of any metallic objects that are embedded or attached to the fabric and helps us to locate and eliminate them.
We also record and document the results of the detection process for traceability and quality assurance purposes.
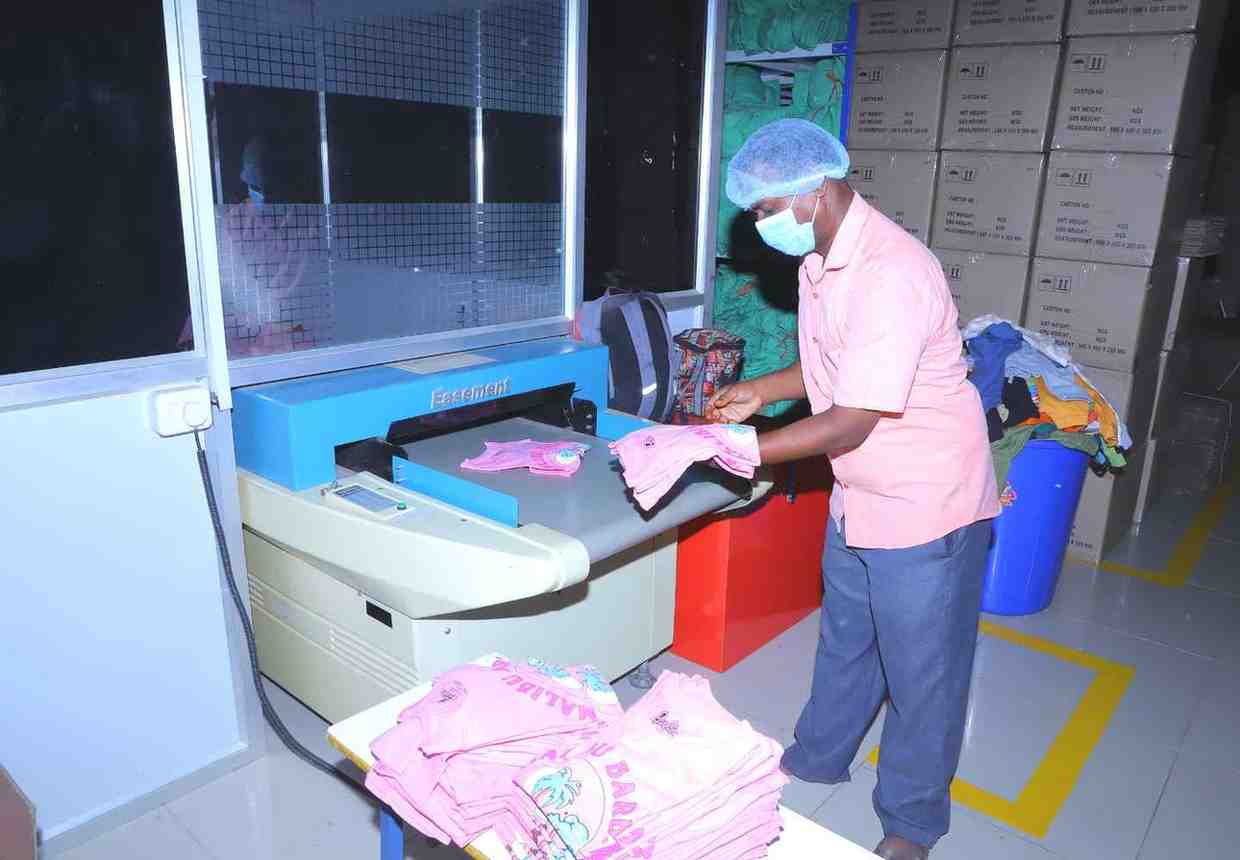
Our quality checking process involves the following steps:
Raw material inspection
We source our raw materials from reputed suppliers who adhere to international standards of quality and safety. We inspect the raw materials for their color, texture, weight, and durability before using them for production.
In-process inspection
We monitor the production process closely and check every stage of knitting, dyeing, printing, embroidery, and stitching for any errors or deviations. We use advanced machines and equipment that are calibrated and maintained regularly to ensure accuracy and consistency.
Final inspection
We conduct a final inspection of the finished products before packing and dispatching them to our clients. We check the products for their size, fit, appearance, and functionality. We also verify the labels, tags, and packaging materials for their correctness and quality.
We have a team of experienced and skilled quality controllers who perform the quality checking process with utmost care and attention. They use various tools and methods such as visual inspection, measurement, testing, and sampling to ensure the quality of our products. They also follow the quality standards and specifications provided by our clients and comply with the industry norms and regulations.
We believe that quality is not only a result but also a process. We strive to improve our quality checking process continuously by adopting best practices, implementing feedback, and conducting audits. We aim to achieve customer satisfaction and loyalty by delivering products that are superior in quality and value.